Capabilities
Resourced Nationally
We have strategic alliances with the best flexo converting facilities in the United States. Having a vested interest in these partnerships provides us with the integrated capabilities, capacity, and flexibility to work locally, regionally, or throughout the US. We are truly resourced on a national basis!
Key Plant Characteristics
- Fully integrated state of the art facilities house the latest advances in equipment and processes
- Highly skilled workforce that maximizes these capabilities
- Focus on sustainability through lean manufacturing processes and use of high performance raw materials such as films and inks
- QA programs ensure tight process controls (SQF, AIB)
- Provide turn-key solutions – from laboratory testing, to design, to finished product
- Primary Locations –
- Flexo: IL, NC, TX
- Digital: OH, IL
- Extrusion: NC
Flexsource Advanced Capabilities
Printing
Printing
Lamination
Slitting
Conversion
Extrusion
Flexsource
Printing
We have the flexibility to use different printing processes based on the requirements of your particular job, and conduct all initial press checks to ensure complete satisfaction with color match.
Standard Flexography
(designed for longer runs)
- Up to 10 color high-end process printing
- 150 Line screen available
- presses up to 75″ wide
- Surface and reverse printing
- Matte/Gloss combination
- Shrink PE films available
- Scuff resistant and UV applications
- Microwaveable & Oven-able applications
Digital Printing
(best suited for short runs, multiple SKUs, speed to market, no plate charges)
- Up to 30” web widths
- Variable Data Printing (VDP) – ability to print unique text and graphics on each and every package
- Photo quality images that typically surpasses that of flexography
- 100% color consistency
- Perfect registration
Flexsource
Printing
We have the flexibility to use different printing processes based on the requirements of your particular job, and conduct all initial press checks to ensure complete satisfaction with color match.
Standard Flexography
(designed for longer runs)
- Up to 10 color high-end process printing
- 150 Line screen available
- presses up to 75″ wide
- Surface and reverse printing
- Matte/Gloss combination
- Shrink PE films available
- Scuff resistant and UV applications
- Microwaveable & Oven-able applications
Digital Printing
(best suited for short runs, multiple SKUs, speed to market, no plate charges)
- Up to 30” web widths
- Variable Data Printing (VDP) – ability to print unique text and graphics on each and every package
- Photo quality images that typically surpasses that of flexography
- 100% color consistency
- Perfect registration
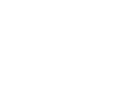
Flexsource
Lamination
Solventless Adhesive Laminations (SAL) which cure fast, and are more eco-friendly than alternative processes
2, 3 and 4 Ply structures available
Ability to work with all popular film structures
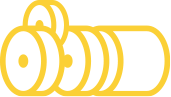
Flexsource
Slitting
Precision slitting up to 8 Mil
Narrow web available
Large ODs available
Tight tolerances / clean roll edges
3” and 6” cores
Recycle all edge trim
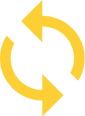
Flexsource
Conversion
Printed Roll-Stock for HFFS/VFFS applications
- Available with pre-applied zippers, laser scoring, and macro/micro perforations
POUCHES
- Stand-up Pouches & 2/3 Side Seal Pouches
- Available in most popular styles and features
- Liquid Tight and Leak Proof options
CUSTOM BAGS
- Standard and custom sizes and configurations available
- Recloseable
- Compartment
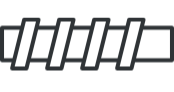
Flexsource
Extrusion
6 extrusion lines
- Four mono-layer lines
- One 3 layer line
- One 5 layer line
Types of films produced
- Monolayer PE, LLD/PE blends, Metallocene blends, EVA blends
- Multi-layers including Co-extruded films for various applications
- Colors available